Public
Pretium Packaging 3D Catalog
Pretium Packaging Catalog
Pretium Packaging Locations
Pretium Packaging Market Gallery
Pretium Packaging News & Events
Pretium Packaging PDF Catalogs
Pretium Packaging Videos
Pretium Showcase 3D Products
If this is your company, CONTACT US to activate Packbase™ software to build your portal.
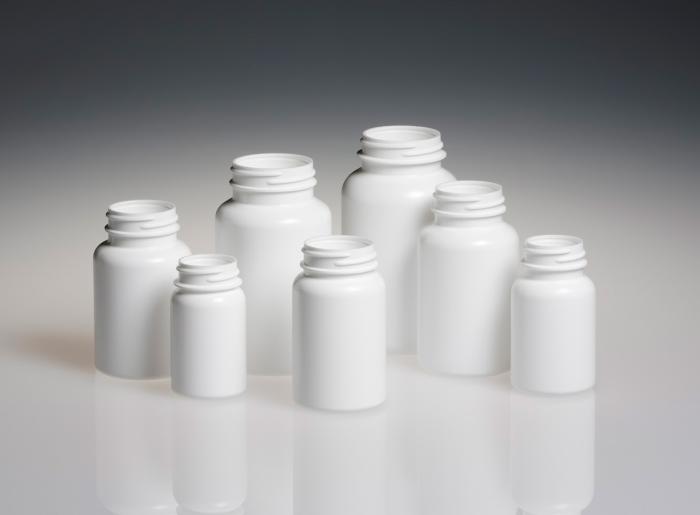

Alpha Packaging has just qualified six new injection blow molded high density polyethylene (HDPE) packers as part of its new HDPE Pharma Line. When completed later this fall, Alpha’s Pharma Line will consist of more than a dozen injection blow molded and extrusion blow molded bottles that replicate the HDPE round bottles most prevalent in the pharmaceutical industry. The new line is also ideal for Alpha’s core customer base of nutritional supplement manufacturers and fillers – many of which are located on the East Coast near Alpha’s Bethlehem, Penn., manufacturing site.
Rather than replicating its own existing HDPE lines or simply moving assets from other plants, Alpha is investing in brand-new IBM and EBM machines and new molds for more than a dozen sizes of bottles, ranging from 50cc to 950cc. Sizes up to 300cc will be manufactured on brand new equipment using the Injection Blow Molding process. Larger sizes will be Extrusion Blow Molded on new equipment with brand new blow molds. Production lines will also feature state-of-the art vision systems and leak detectors. Alpha is investing more than $3.5 million in new machines, molds and downstream equipment for Phase I of the new HDPE cell, and is prepared to double or triple that investment in 2014.
Brian McCarthy, Vice President of Sales and New Business Development, says the new capacity will help Alpha grow with existing customers, and also open up new opportunities with pharmaceutical manufacturers. “Alpha’s mission in developing this new line of HDPE Pharma Line Packers is to offer nutritional supplement brands, contract fillers and generic and branded pharmaceutical companies a complete line of HDPE bottles that matches their current specifications. This will facilitate a more seamless transition to Alpha’s Pharma line.” McCarthy says. “We will have at least 14 sizes of Pharma Line bottles by the end of 2013 at our East Coast facility, as well as other popular HDPE rounds, oblongs and squares.” McCarthy says many Alpha customers have already committed to converting their business from other Alpha plants to the new Bethlehem HDPE cell, and he expects more customers to convert as more packer sizes are qualified. Alpha has stock of the Pharma Line bottles in 50cc, 75cc, 100cc, 120cc, 150cc, 225cc and 275cc sizes, all of which are available now to purchase. It will also introduce 180cc and 300cc sizes in August. In September, a 12-cavity EBM machine with 125mm centers will be qualified, and at least five additional bottles, 400cc and larger, will be available before the end of the year.
In addition to the new line of HDPE packers, the high-cavity, large output extrusion platform will allow Alpha to capture custom packaging projects for personal care, household chemicals and automotive products. “We have invested in high cavitation to keep up with industry demand and offer a state-of-the-art packer line at competitive pricing,” McCarthy says, “but the nutrition and pharma industries will not be our only targets. This new EBM platform in particular will make us very competitive in East Coast personal care as well, and complement our existing capabilities.”
Alpha’s manufacturing processes integrate the finest Food and Drug Administration-approved raw materials with state-of-the-art equipment and stringent quality control processes. All manufacturing and warehousing is conducted in sealed, clean, controlled environments. Most manufacturing lines include leak detectors and vision systems installed in-line. For the new HDPE packer line, most bottle sizes will be available in either carton packs or bulk bags, which allow customers to get a more efficient pack-out for optimum utilization of trucks. Alpha’s East Coast customers will also benefit from lower shipping costs and a better environmental footprint when they purchase bottles made in Alpha’s Bethlehem plant.
Alpha’s President and Chief Executive Officer, Jeff Kellar, says Alpha is one of the few North American companies in the packaging industry that is reinvesting in new equipment and capacity. “We are working closely in partnership with key customers to invest in the technologies and blow molds that support their growth,” Kellar says. “With this additional capacity, we’ve increased our ability to serve our primary markets such as nutritional, pharmaceutical and personal care. Our continued expansion reinforces our commitment to offer the best quality and speed to market with one of the largest portfolios of stock and custom bottles in the industry.”
Kellar says the new HDPE cell is a good example of how Alpha is able to manage complexity and provide customers with a level of service that other manufacturers cannot. “By adding this new capability on the East Coast, Alpha is filling a gap in the market that other companies have not managed to fill.” Many of the customers targeted for the new HDPE Pharma Line are already buying Alpha’s polyethylene terephthalate (PET) vitamin packers, so the new HDPE capacity will allow these customers to consolidate their HDPE and PET packers into full truckloads from one FOB location. “Customers can leverage their purchases to get better shipping rates on fully-utilized trucks, and also improve their sustainability at the same time,” he says.